What is Porosity in Welding: Understanding Its Causes and Enhancing Your Skills
What is Porosity in Welding: Understanding Its Causes and Enhancing Your Skills
Blog Article
Porosity in Welding: Identifying Common Issues and Implementing Best Practices for Avoidance
Porosity in welding is a pervasive concern that typically goes undetected up until it causes substantial problems with the stability of welds. This common flaw can compromise the stamina and resilience of welded structures, presenting safety dangers and bring about costly rework. By recognizing the origin of porosity and applying effective prevention approaches, welders can considerably enhance the top quality and reliability of their welds. In this discussion, we will check out the vital factors adding to porosity formation, examine its damaging results on weld performance, and talk about the very best techniques that can be taken on to minimize porosity incident in welding procedures.
Usual Sources Of Porosity
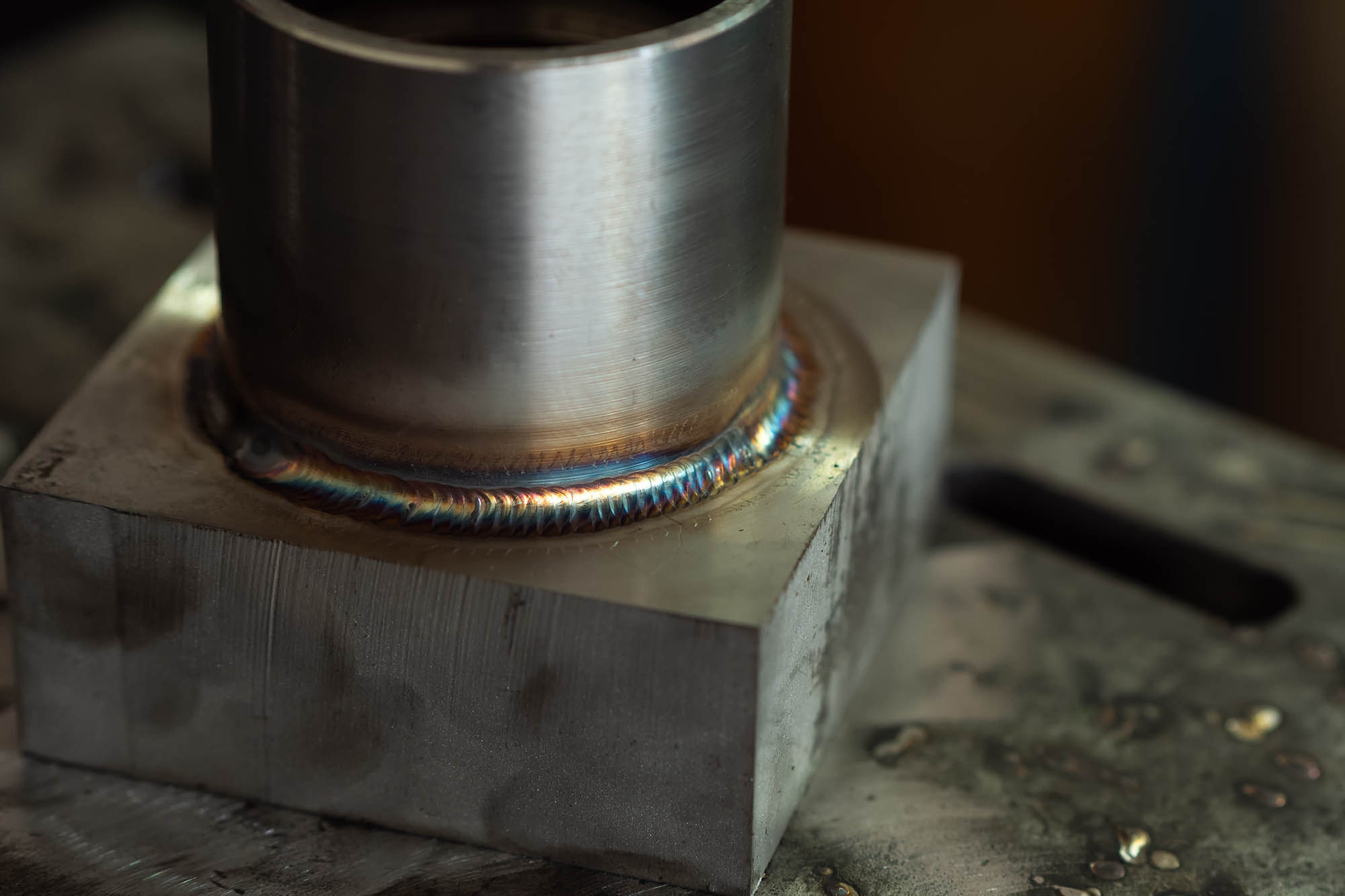
Utilizing filthy or wet filler materials can present contaminations right into the weld, adding to porosity concerns. To minimize these usual reasons of porosity, detailed cleansing of base steels, correct securing gas option, and adherence to optimum welding criteria are essential practices in attaining high-quality, porosity-free welds.
Effect of Porosity on Weld High Quality

The existence of porosity in welding can substantially compromise the architectural honesty and mechanical homes of welded joints. Porosity develops gaps within the weld metal, damaging its total stamina and load-bearing capacity. These gaps function as tension concentration factors, making the weld a lot more vulnerable to cracking and failing under applied lots. Furthermore, porosity can reduce the weld's resistance to deterioration and other environmental aspects, additionally diminishing its long life and performance.
One of the main consequences of porosity is a reduction in the weld's ductility and sturdiness. Welds with high porosity levels often tend to exhibit lower influence strength and minimized capacity to deform plastically before fracturing. This can be specifically concerning in applications where the welded elements are subjected to dynamic or cyclic loading conditions. Furthermore, porosity can hinder the weld's capacity to effectively transfer pressures, bring about premature weld failure and prospective safety and security hazards in critical structures.
Ideal Practices for Porosity Prevention
To improve the structural honesty and high quality of welded joints, what particular measures can be applied to decrease the event of porosity throughout the welding process? Porosity prevention in welding is essential to guarantee the integrity and toughness of the last weld. One efficient technique is appropriate cleaning of the base metal, getting rid of any kind of pollutants such as rust, oil, paint, or dampness that can cause gas entrapment. Making sure that the welding equipment remains in great condition, with tidy consumables and proper gas flow prices, can likewise considerably reduce porosity. In addition, preserving a steady arc and managing the welding parameters, such Full Report as voltage, existing, and travel rate, helps develop a constant weld swimming pool that lessens why not find out more the risk of gas entrapment. Making use of the appropriate welding strategy for the particular product being welded, such as readjusting the welding angle and gun placement, can even more protect against porosity. Routine inspection of welds and instant removal of any type of problems recognized during the welding procedure are vital techniques to avoid porosity and generate premium welds.
Importance of Proper Welding Techniques
Carrying out appropriate welding methods is vital in making sure the architectural honesty and high quality of welded joints, constructing upon the structure of effective porosity prevention steps. Extreme warmth can lead to boosted porosity due to the entrapment of gases in the weld swimming pool. In addition, utilizing the suitable welding parameters, such as voltage, present, and take a trip rate, is vital for attaining sound welds with minimal porosity.
Additionally, the selection of welding process, whether it be MIG, TIG, or stick welding, must align with the certain needs of the project to make sure optimal results. Appropriate cleansing and preparation of the base metal, in addition to picking the best filler product, are additionally essential elements of skillful welding techniques. By adhering to these finest techniques, welders can reduce the danger of porosity development and produce high-quality, structurally sound welds.
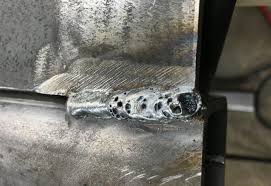
Checking and Quality Assurance Measures
Quality control steps play a critical duty in verifying the integrity and reliability of welded joints. Checking treatments are necessary to identify and protect against porosity in welding, ensuring the toughness and durability of the end product. Non-destructive screening approaches such as ultrasonic testing, radiographic testing, and visual evaluation are typically employed to recognize possible flaws like porosity. These methods enable for the assessment of weld quality without endangering the stability of the joint. What is Porosity.
Carrying out pre-weld and post-weld examinations is likewise critical in preserving quality assurance standards. Pre-weld assessments involve confirming the products, tools setups, and tidiness of the job location to avoid contamination. Post-weld examinations, on the other hand, evaluate the last weld for any kind of defects, including porosity, and verify that it fulfills defined standards. Implementing a detailed quality assurance plan that includes extensive screening treatments and look here examinations is paramount to decreasing porosity problems and making sure the general top quality of bonded joints.
Conclusion
In conclusion, porosity in welding can be a common concern that influences the high quality of welds. By determining the usual root causes of porosity and applying finest methods for avoidance, such as proper welding strategies and testing steps, welders can make sure excellent quality and trustworthy welds. It is necessary to prioritize avoidance techniques to decrease the event of porosity and keep the integrity of bonded structures.
Report this page